How Smarter Compressed Air Management Cut Energy Costs at a Semiconductor Facility
In the high-tech world of semiconductor manufacturing, precision and cleanliness aren’t just desirable—they’re essential. Facilities that produce the silicon wafer slices used in everything from smartphones to solar panels rely heavily on ultra-clean, oil-free compressed air. But what happens when that air comes at a higher-than-necessary cost?
At one major semiconductor plant on the West Coast, IZ Systems uncovered a hidden opportunity: a chance to reduce energy use dramatically without compromising product quality. Here’s how we helped them do it.
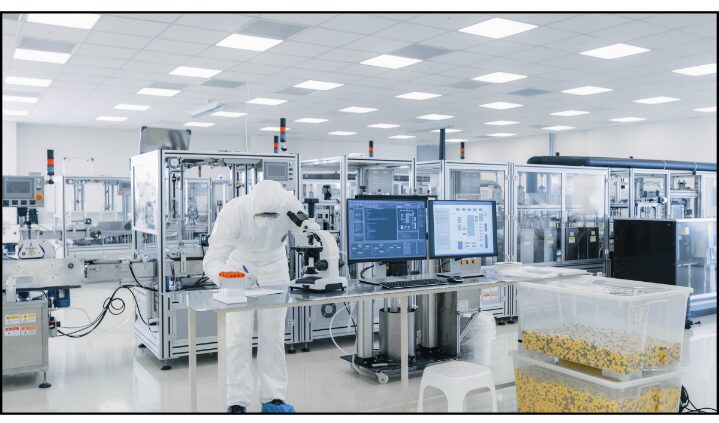
The Challenge: Too Much of a Good Thing
The facility in question relied on six large, 300-horsepower oil-free screw compressors. Each compressor was paired with a heatless desiccant dryer, designed to remove moisture from the air. These systems were delivering air at an ultra-low -100°F pressure dewpoint—a level of dryness well beyond what most industrial processes actually need.
While that might sound like a good thing, there was a catch. Maintaining such an ultra-dry dewpoint required a purge rate of 20%, meaning a significant portion of the compressed air was constantly being vented just to keep the system that dry. And with California’s high energy costs, that meant a lot of wasted electricity and money.
When we analyzed the data from the system’s logging equipment, the inefficiency was clear: the desiccant dryer purge cycles were dictating compressor loading—essentially making the compressors work harder than necessary around the clock.
Digging Deeper: Is -100°F Really Necessary?
We often find that dewpoint specifications in compressed air systems are based more on the capabilities of the equipment than on actual process requirements. That turned out to be the case here.
Because the dry air was being used to help remove residual oil and moisture from the wafers, everyone assumed that -100°F was needed to protect product quality. But when we installed dewpoint sensors throughout the system, the real picture came into focus.
The -100°F dewpoint was only present right at the dryer outlets. Downstream, in the facility’s air distribution headers, dewpoints were significantly higher—suggesting the ultra-dry air wasn’t staying that dry once it entered the system.
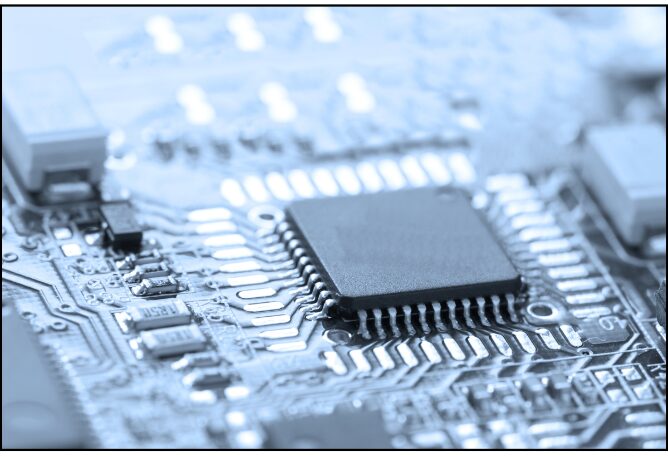
The Solution: A Smarter, More Flexible Design
To tackle the problem, we redesigned the air system with flexibility and control in mind.
We created a “wet header” that feeds a shared bank of existing dryers. This setup allows the system to adjust to changing compressor loads without compromising dewpoint control. Multiple dryers can now support fewer compressors, resulting in:
- Lower pressure drop across the system
- Reduced compressor pressure setpoints
- Less energy consumption overall
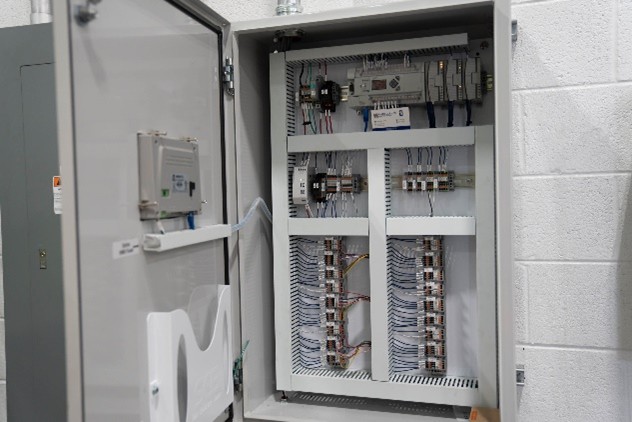
To give the system even more adaptability, we installed dewpoint controls on the dryers, allowing purge cycles to respond to actual moisture levels—not just a fixed setting. We also added automated valves at each dryer, so any unit could be taken offline for maintenance or energy savings, and brought back online instantly without upsetting the dewpoint balance.
An integrated automation system was the final piece of the puzzle. It now manages compressor operation, monitors dewpoint, and coordinates dryer performance—all in real-time.
The Result: Big Energy Wins, Zero Product Impact
The real magic happened when we began gradually increasing the target dewpoint using the automation system—while the facility monitored product quality closely.
The outcome? No negative effects on the wafers, even with the dewpoint set as high as 0°F. That’s a 100-degree swing from the original spec.
With the new system in place and dewpoint settings optimized, the plant was able to shut down over 660 horsepower worth of compressors—without sacrificing redundancy or risking downtime.
To top it off, the facility earned a significant energy incentive from its local utility, which helped cover the cost of the retrofit. The return on investment? Less than one year.
The Takeaway: Don’t Let Old Assumptions Drive Today’s Energy Use
Compressed air is a critical utility in semiconductor manufacturing, but it doesn’t have to be an energy hog. As this project proved, understanding what your process actually needs—and designing controls to meet those needs dynamically—can unlock major savings.
For facilities chasing both precision and efficiency, smarter compressed air management may be one of the easiest wins on the table.